NON - VIGOROUS HEADLOSS EQUATION
The empirical equation which are Hazen-William, Manning and Darcy Weisbach were arranged into the form of head loss equation
Darcy Weisbach
Darcy–Weisbach equation is a phenomenological equation, which relates the head loss — or pressure loss due to friction along a given length of pipe to the average velocity of the fluid flow. The equation is named after Henry Darcy and Julius Weisbach
The Darcy-Weisbach equation is valid for fully developed, steady state and incompressible flow. The friction factor or coefficient, λ -depends on the flow, if it is laminar or turbulent (the Reynolds Number) - and the roughness of the tube or duct. The friction coefficient can be calculated by using the Moody Diagram.
For this, it is necessary to substitute the following into the original head loss form of the Darcy–Weisbach equation

where
For the general case of an arbitrarily-full pipe, the value of Aw will not be immediately known, being an implicit function of pipe slope, cross-sectional shape, flow rate and other variables. If, however, the pipe is assumed to be full flowing and of circular cross-section, as is common in practical scenarios, then

By substituting the original formulation yields the final equation for head loss in terms of volumetric flow rate in a full-flowing circular pipe. The equation below are defined.
Hazen - William
Hazen–Williams equation is an empirical relationship which relates the flow of water in a pipe with the physical properties of the pipe and the pressure drop caused by friction. It is used in the design of water pipe systems such as fire sprinkle systems, water supply networks, and irrigation systems. It is named after Allen Hazen and Gardner Stewart Williams.
The Hazen–Williams equation has the advantage that the coefficient C is not a function of the Reynold's Number, but it has the disadvantage that it is only valid for water. Also, it does not account for the temperature or viscosity of the water
The Darcy-Weisbach equation was difficult to use because the friction factor was difficult to estimate.The general form of the equation relates the mean velocity of water in a pipe with the geometric properties of the pipe and slope of the energy line.
- V is velocity
- k is a conversion factor for the unit system (k = 1.318 for US customary units, k = 0.849 for SI units)
- C is a roughness coefficient
- R is the hydraulic radius
- S is the slope of the energy line head loss per length of pipe or hf/L
When used to calculate the head loss with the International System of Units, the equation becomes
Manning
Manning formula is also known as the Gauckler-Manning Formula or Gauckler–Manning–Strickler formula in Europe. In the United States, in practice, it is very frequently called simply Manning's Equation. The Manning formula is an empirical formula estimating the average velocity of a liquid flowing in a conduit that does not completely enclose the liquid. All flow in so-called open channels is driven by gravity. It was first presented by the French engineer Philippe Gauckler in 1867, and later re-developed by the Irish engineer Robert Manning.
The Gauckler–Manning formula states:
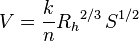
where:
- V is the cross-sectional average velocity (L/T; ft/s, m/s);
- n is the Gauckler–Manning coefficient. Units for values of n are often left off, however it is not dimensionless, having units of: (T/[L1/3]; s/[ft1/3]; s/[m1/3]).
- Rh is the hydraulic radius (L; ft, m);
- S is the slope of the hydraulic grade line or the linear hydraulic head loss (L/L), which is the same as the channel bed slope when the water depth is constant. (S = hf/L).
- k is a conversion factor between SI and English units. It can be left out if consistent units are used throughout. However it is standard practice to use k=1 for SI units, and k=1.49 for English units. (Note: (1 m)1/3/s = (3.2808399 ft) 1/3/s = 1.4859 ft1/3/s)
NOTE: Ks strickler = 1/n manning. The coefficient Ks strickler varies from 20 (rough stone and rough surface) to 80 m1/3/s (smooth concrete and cast iron).
The discharge formula, Q = A V, can be used to manipulate Gauckler–Manning's equation by substitution for V. Solving for Q then allows an estimate of the volumetric flow rate(discharge) without knowing the limiting or actual flow velocity.
The equation then now is being used as a Manning headloss equation,
by : AmiraHaris
Past . Future
MechasFluid

This is all about Pipe System.
CONCLUSION
Piping systems are documented in piping and instrumentation diagrams (P&IDs). If necessary, pipes can be cleaned by the tube cleaning process. Within industry, piping is a system of pipes used to convey fluids (liquids and gases) from one location to another. The engineering discipline of piping design studies the efficient transport of fluid.
"Piping" sometimes refers to Piping Design, the detailed specification of the physical piping layout within a process plant or commercial building. In earlier days, this was sometimes called Drafting, Technical drawing, Engineering Drawing, and Design but is today commonly performed by Designers who have learned to use automated Computer Aided Drawing / Computer Aided Design (CAD) software.
Plumbing is a piping system with which most people are familiar, as it constitutes the form of fluid transportation that is used to provide potable water and fuels to their homes and businesses. Plumbing pipes also remove waste in the form of sewage, and allow venting of sewage gases to the outdoors. Fire sprinkler systems also use piping, and may transport nonpotable or potable water, or other fire-suppression fluids.
Piping also has many other industrial applications, which are crucial for moving raw and semi-processed fluids for refining into more useful products. Some of the more exotic materials of construction are Inconel, titanium, chrome-moly and various other steel alloys.
REFERENCES
-Çengel, A. Yusof. Cimbala, M. John (2014). Fluid Mechanics. Singapore: Mc Graw Hill Education
-Douglas J. F. 2005. Fluid Mechanics. Pearson 5th Edition.
-Sturm T. W. 2001. Open Channel Hydraulics; McGraw-Hill. UK.
-Jain S. C. 2001. Open Channel Flow. John Wiley & Sons.
-Chin D.A. 2000. Water Resources Engineering. Prentice Hall.
-Subramanya K., 1997. Flow in Open Channels. Tata McGraw-Hill, New Delhi.
-Fluid Mechanics Module, Penerbit UTHM, Noor Aliza Ahmad, Roslinda Seswoya & Zarina Md Al
-(2009, Nov). Fluid Mechanics. Retrieved from http://en.wikipedia.org/wiki/Fluid_mechanics
-(2015,May). Pipe network analysis. Retrieved from http://en.wikipedia.org/wiki/Pipe_network_analysis
-(2011, June). Branching pipe. Retrieved from http://www.unimasr.net/
-(2010, August). Pipe in series and parallel. Retrieved from http://nptel.ac.in/courses/112104118/lecture-36/36-1_flow_through_branched_pipe.htm
GROUP MEMBERS


Emaz Zulaiha Binti Ismail
AF140071

Amira NurHayati Binti Haris
AF140023

Zafirah Binti Jamil
AF140053

Eny Nor Syahira Binti Singkaru @ Mohamad Hashim
AF130165
|